در این مقاله قصد داریم در مورد مراحل تولید سیم و کابل از مفتول مسی یا آلومینیوم تا بسته بندی توضیحاتی ارائه دهیم و یک پیش زمینه در رابطه با دستگاههای مورد استفاده نیز در اختیارتان بگذاریم.
تولید سیم و کابل یک فرآیند پیچیده است که شامل چندین مرحله است. این مراحل از آمادهسازی مواد اولیه تا بستهبندی محصول نهایی را شامل میشود. در ادامه به بررسی دقیقتر هر یک از این مراحل میپردازیم:
۱. تهیه مواد اولیه
- فلزات هادی: معمولاً مس یا آلومینیوم به عنوان هادی اصلی در سیمها و کابلها استفاده میشود. این فلزات به دلیل رسانایی الکتریکی بالا و مقاومت در برابر خوردگی انتخاب میشوند.
- عایقها: مواد عایقی مانند PVC، XLPE، لاستیک و … برای پوشش سیمها استفاده میشوند تا از اتصال کوتاه و برقگرفتگی جلوگیری شود.
- روکشها: روکشهای خارجی کابلها معمولاً از جنس PVC، پلیاتیلن یا مواد دیگر ساخته میشوند تا از کابل در برابر عوامل محیطی مانند رطوبت، حرارت و آسیبهای مکانیکی محافظت کنند.
۲. نازککاری مفتول
- مفتولهای فلزی (مس یا آلومینیوم) با ضخامت مشخص تهیه شده و از طریق دستگاههای کشش به قطر مورد نظر میرسند.
- این مرحله بسیار مهم است زیرا قطر مفتولها بر روی خواص نهایی سیم و کابل تأثیر مستقیم دارد.
۳. آنیل کردن
- پس از نازککاری، مفتولها به مدت مشخص در دمای بالا حرارت داده میشوند (آنیل کردن) تا تنشهای داخلی ایجاد شده در حین کشش از بین برود و قابلیت شکلپذیری آنها افزایش یابد.
۴. استرند کردن
- چندین مفتول نازک به صورت موازی به هم تابیده میشوند تا یک رشته (استرند) تشکیل دهند. این کار باعث افزایش انعطافپذیری و کاهش اثر پوستی میشود.
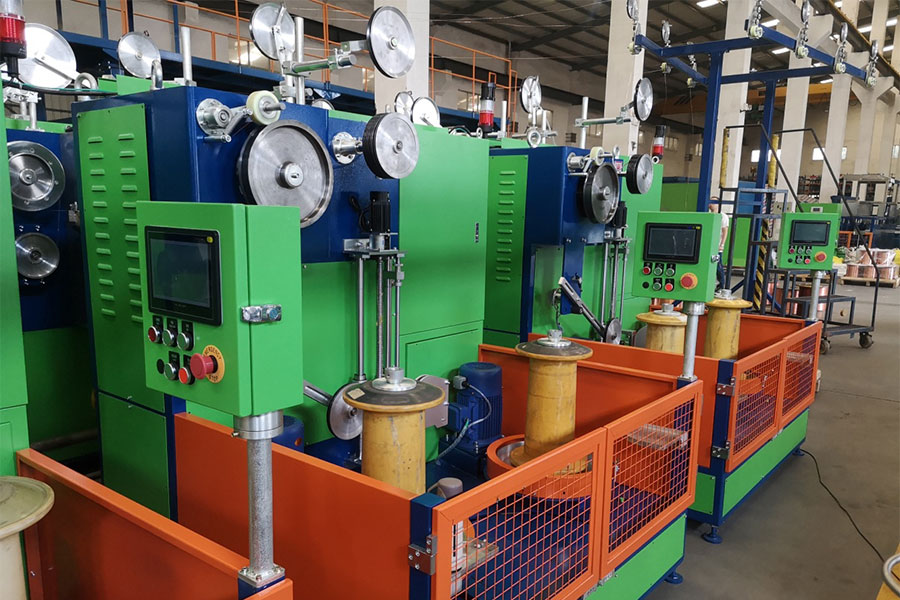
۵. اکسترود کردن عایق
- رشتههای تابیده شده (استرندها) از داخل دستگاه اکسترودر عبور داده میشوند و یک لایه عایق به دور آنها کشیده میشود.
- نوع عایق و ضخامت آن به ولتاژ و کاربرد کابل بستگی دارد.
۶. روکشزنی
- روی لایه عایق، یک لایه روکش اضافه میشود تا از کابل در برابر عوامل محیطی محافظت کند.
- روکش میتواند تک رنگ یا چند رنگ باشد و علائم مشخصی روی آن حک شود تا شناسایی کابل آسانتر شود.
۷. چاپ و مارکزنی
- روی روکش کابل، مشخصاتی مانند نوع کابل، ولتاژ، تعداد رشتهها، تاریخ تولید و … چاپ میشود.
۸. آزمون و کنترل کیفیت
- در این مرحله، کابلهای تولید شده از نظر مقاومت الکتریکی، عایقی، مکانیکی و شیمیایی مورد آزمایش قرار میگیرند تا مطابق با استانداردهای تعیین شده باشند.
۹. بستهبندی
- کابلهای بازرسی شده به صورت قرقره یا رول بستهبندی شده و برای حمل و نقل آماده میشوند.
عوامل موثر بر کیفیت سیم و کابل:
- مواد اولیه: کیفیت مواد اولیه به طور مستقیم بر عمر مفید و عملکرد کابل تأثیر میگذارد.
- فرآیند تولید: رعایت دقیق مراحل تولید و استفاده از تجهیزات مدرن باعث تولید کابلهای با کیفیت میشود.
- کنترل کیفیت: انجام آزمایشهای دقیق در طول فرآیند تولید و پس از آن، از تولید محصولات با کیفیت اطمینان حاصل میکند.
استانداردهای تولید سیم و کابل
تولید سیم و کابل باید مطابق با استانداردهای ملی و بینالمللی انجام شود. برخی از مهمترین استانداردها عبارتند از:
- استاندارد IEC (کمیسیون بینالمللی الکتروتکنیک)
- استاندارد ملی ایران (ISIRI)
توجه: این مراحل به صورت کلی بیان شده و ممکن است بسته به نوع کابل و تکنولوژی مورد استفاده، تفاوتهایی در جزئیات وجود داشته باشد.
انواع عایقهای اکسترود شده روی مفتولها و کابلها
عایقها نقش حیاتی در محافظت از هادیهای الکتریکی در برابر آسیبهای فیزیکی، شیمیایی و محیطی ایفا میکنند. فرآیند اکستروژن، روشی موثر برای پوشش دادن هادیها با لایههای یکنواخت و پیوسته از مواد عایقی است. در ادامه به بررسی انواع مختلف عایقهای اکسترود شده که معمولاً در تولید سیمها و کابلها استفاده میشوند، میپردازیم:
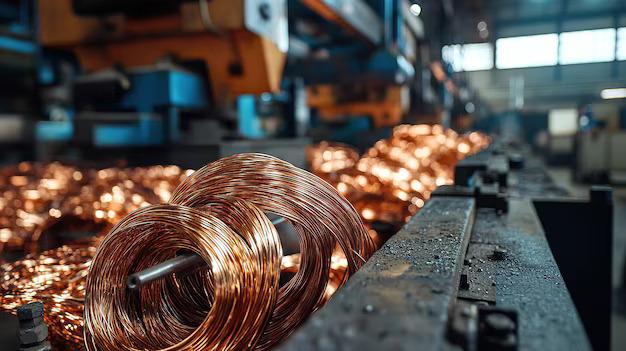
۱. پلیوینیل کلراید (PVC)
- ویژگیها: PVC یکی از رایجترین مواد عایقی است. ارزان، انعطافپذیر، مقاوم در برابر مواد شیمیایی و رطوبت است.
- کاربردها: در کابلهای برق با ولتاژ پایین، کابلهای کنترل، کابلهای ساختمانی و سیمهای روکشدار استفاده میشود.
۲. پلیاتیلن (PE)
- ویژگیها: PE عایقی با خواص الکتریکی خوب، مقاومت در برابر رطوبت و مواد شیمیایی است. انعطافپذیری بالایی دارد و در دماهای پایین نیز عملکرد خوبی از خود نشان میدهد.
- کاربردها: در کابلهای برق با ولتاژ متوسط، کابلهای زیرزمینی، کابلهای دریایی و کابلهای ارتباطی استفاده میشود.
۳. پلیاتیلن شبکهای شده (XLPE)
- ویژگیها: XLPE از طریق فرآیند شبکهای شدن، خواص مکانیکی و حرارتی بهتری نسبت به PE معمولی دارد. مقاومت الکتریکی بالا، مقاومت در برابر حرارت و رطوبت از مزایای آن است.
- کاربردها: در کابلهای برق با ولتاژ متوسط و بالا، کابلهای زیرزمینی و کابلهای دریایی استفاده میشود.
۴. لاستیک
- ویژگیها: لاستیک طبیعی و مصنوعی به عنوان عایق در برابر سایش، روغن و مواد شیمیایی مقاوم هستند. انعطافپذیری بالایی دارند و در دماهای بالا و پایین عملکرد خوبی از خود نشان میدهند.
- کاربردها: در کابلهای صنعتی، کابلهای خودنگهدار و کابلهای مخصوص محیطهای خشن استفاده میشوند.
۵. پلیتترافلوئرواتیلن (PTFE)
- ویژگیها: PTFE یا تفلون، عایقی با مقاومت حرارتی بسیار بالا، مقاومت شیمیایی عالی و خواص الکتریکی فوقالعاده است.
- کاربردها: در کابلهای مخصوص کاربرد در دمای بالا، کابلهای صنایع شیمیایی و کابلهای الکترونیکی استفاده میشود.
۶. ترموپلاستیک الاستومر (TPE)
- ویژگیها: TPE ترکیبی از خواص پلاستیکها و لاستیکها است. انعطافپذیر، سبک و مقاوم در برابر سایش و مواد شیمیایی است.
- کاربردها: در کابلهای کنترل، کابلهای حسگر و کابلهای مخصوص کاربردهای خاص استفاده میشود.
عوامل موثر در انتخاب نوع عایق
- ولتاژ: هر عایق برای محدوده ولتاژی مشخصی مناسب است.
- دما: دمای محیط کار و دمای کاری کابل در انتخاب عایق موثر است.
- محیط: شرایط محیطی مانند رطوبت، مواد شیمیایی و عوامل مکانیکی در انتخاب عایق موثر هستند.
- انعطافپذیری: نیاز به انعطافپذیری کابل در انتخاب عایق موثر است.
- هزینه: هزینه مواد عایقی نیز در انتخاب موثر است.